The Quality Management System and certifications behind XUND
Quality management and becoming a class IIa-certified medical device have been the central driving force for the success of XUND from day one. Making quality a priority ensures our products work the way they're supposed to. For our Symptom Check and Illness Check, this means accurately checking your symptoms or assessing the likelihood of a specific condition, providing reliable insights into potential causes, identifying health risks even before the first symptoms appear, and helping you take the right next steps.
We spoke to our Head of Quality, Sophie Pingitzer, and Digital Product Manager, Christoph Jirik about why we decided to become a medical device manufacturer, what our process looks like, and much much more.
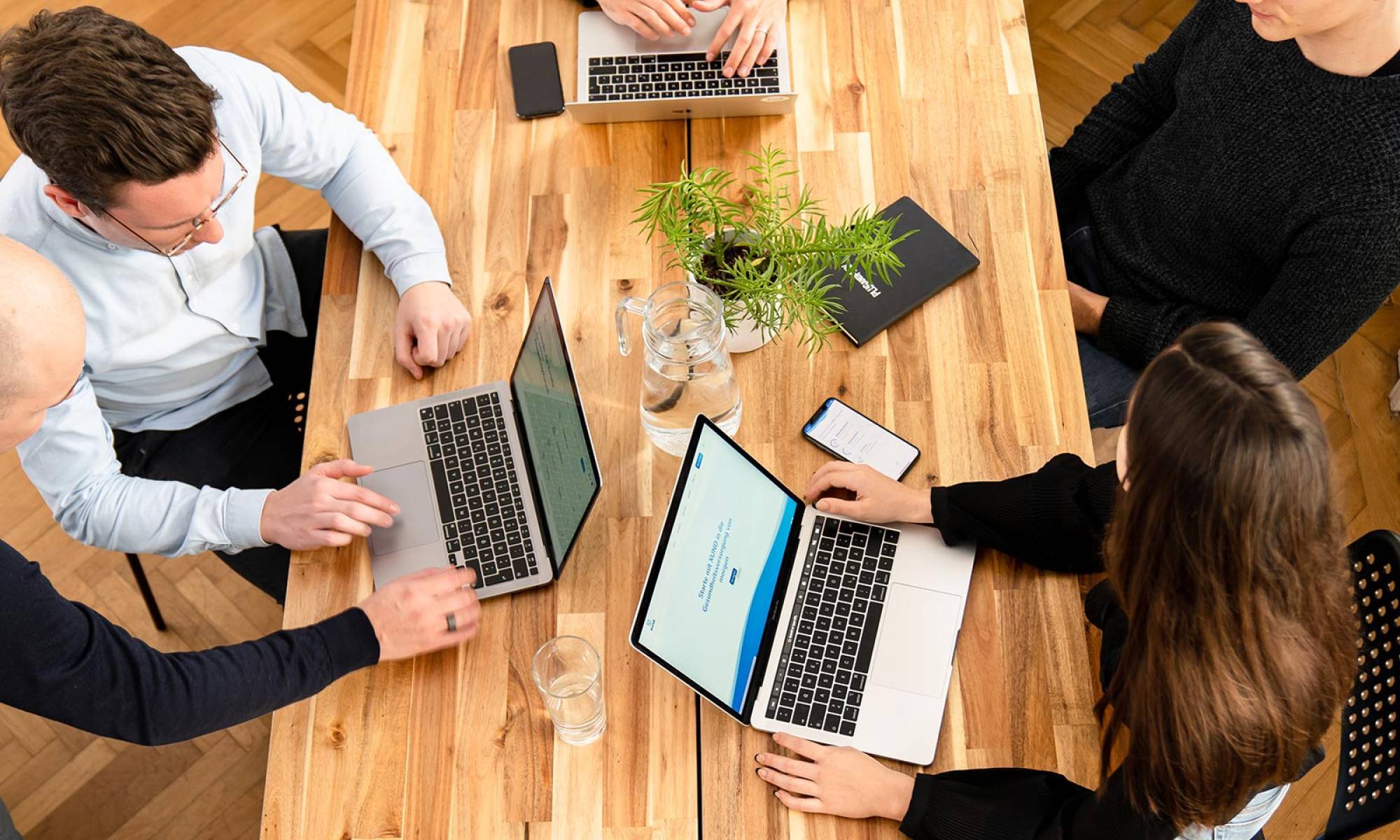
Why a solid Quality Management System (QMS) is healthy for the company, not just the product
Having a solid QMS is the baseline for becoming a medical device manufacturer. Setting it up takes time and resources, and if not set up correctly, it can slow down your development. But our Founders truly understood why it makes sense to implement a QMS from the very beginning. They knew its positive effects would reach way beyond the medical products.
It positively impacts how we recruit and assess people, onboard our team, handle sensitive data, and how we improve our decision-making. Which doesn’t just make sense in medical device terms, but as a business too. Having our Medical API certified as a class IIa medical device gives our partners the trust they need to know that our product doesn’t just work now, but also in the future — provided by a stable and mature company. But not just that: The CE mark demonstrates compliance with the Medical Device Regulation, and an EU-MDR certification ensures the highest possible safety and effectiveness of a medical device in its category.
We have been documenting every single process since day one and have a dedicated team of Quality Managers who are solely focused on building and continuously improving our system. This is also why we managed to be one of the first healthcare technology companies to bring a class IIa medical device to market, in just less than a year after the Medical Device Regulation (MDR) came into effect.
What the QMS process looks like at XUND
Although quality management is central to the development of our technology, ultimately it’s a set of processes across all areas of the company. For example, we have processes in place for:
- Product: how we develop and ship our technology
- People: how we recruit, onboard, and train our team
- Documentation: how we handle documentation and where we store our information
Quality management adds a layer on top of everything. Ensuring the highest quality is a lot about documentation. Whether it’s a decision we made or a bug that was fixed, we need to document it to demonstrate our compliance with regulations.
Our certifications: ISO 13485 and more
Our entire company is certified according to both ISO 13485:2016 and the Medical Device Regulation (MDR), and our Medical API is CE-marked. This is what these certifications ultimately stand for:
- CE mark for the class IIa medical device — demonstrates product conformity
- ISO 13485 & MDR certification — certifies our QMS
- ISO 27001:2013 — certifies our ISMS
As a medical device manufacturer, we must comply with numerous regulatory requirements, which we ensure by adhering to specific industry standards.
In addition to the ISO 13485-compliant QMS, we also meet the requirements of the following relevant national standards, directives, and laws:
- Medical Devices Act and relevant regulations
- EN ISO 14971:2019
- IEC 62304:2006 + A1:2015
- IEC 62366-1:2015
- IEC 82304-1:2016
- EN ISO 15223-1:2021
- ISO 20417:2021
We also comply with all local regulations in countries where we market our product
Medical devices are regulated in the EU by the MDR, which came into force in 2021. With the new rules, the EU set up a stronger regulatory framework aimed at protecting public health and ensuring patient safety. XUND was the first in its industry to gain a class IIa certification for its product. For us, this now means that our technology is analyzed and certified by a Notified Body — TÜV Süd — which holds our product to an even higher standard.
The challenges of certifying a medical device
Certifying technology as a medical device isn’t always easy. The main difficulty being that technology and its development are extremely fast-paced, whereas Notified Bodies and the regulatory system can be a lot stiffer. It's important to acknowledge that the digitization of healthcare is inevitable, and it is a fast and ongoing process. Regulatory frameworks play a pivotal role in guaranteeing quality and safety as innovative products enter the market. Learn more about our perspectives on the hospital of the future here.
Cybersecurity is much more complex when it comes to developing software as opposed to physical medical devices such as scalpels. Disruptive technologies such as AI or Machine Learning also pose major challenges. With the Artificial Intelligence Act, which came into force in 2024, the European Commission has introduced standardized regulations across the EU to address some of these challenges. At XUND, we ensure the safety of our products by maintaining a certified Information Security Management System according to ISO 27001:2013.
It’s also been challenging to raise awareness that maintaining, documenting, and continuously improving the software development process is vital to our success. However, we’ve achieved significant progress here at XUND, and the entire development team is now fully committed.
What our quality management team is working on right now
“Right now, we have a QMS that is stable, robust, and has successfully gotten us the certifications we need to act as a medical device in Europe. Our next step is to make the QMS even more scalable. As we move into international markets, we face different regulations and need to adapt — so that will continue to be one of our main focuses throughout the next months and years. We’re also growing a lot in terms of our team, so we need to align our system with our teams as well, which is exciting. I’m looking forward to it.” — Sophie, Head of Quality
Want to learn more about the team behind our QMS? Follow this link to our interview with Sophie and Christoph.